Electric Heat a quick look at the facilities and products of Rama Industrial Heater Company
RAMA Industrial Heater Company serves widely diversified industries throughout the nation. Today RAMAproducts are providing reliable electric heat for aerospace and aircraft applications . . . for plastics, petroleum and paper processing . . . for packaging, electronic, typographical, laundry, refrigeration, and medical equipment. . . for food processing . . . for tire manufacturing and recapping . . . for use in the refractory, metal fabrication, chemical and cryogenic industries . . . for use in vending, stamping and marking, electrical testing and copying equipment . . . and in literally thousands of other applications. Whenever electric heat is needed . . . look to RAMA!
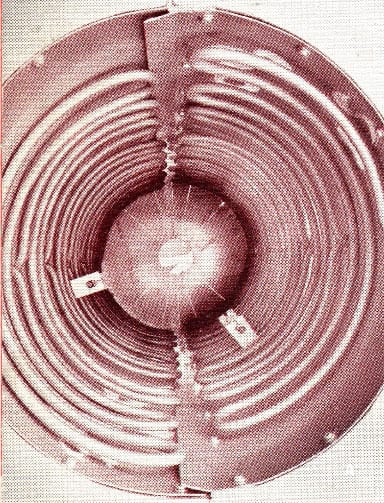
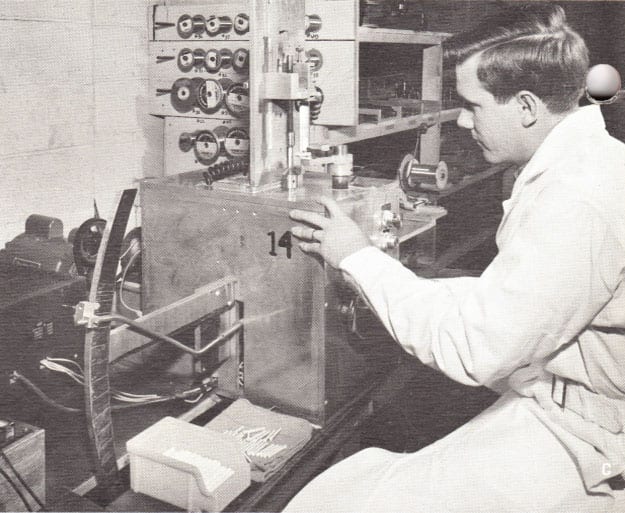
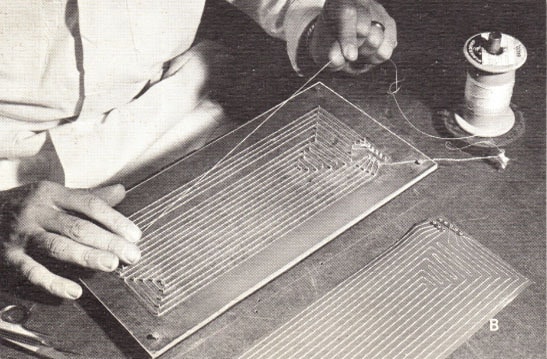
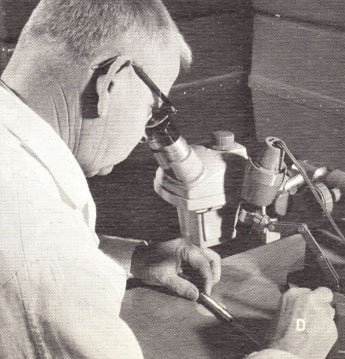
THIS IS RAMA . . . specialists in industrial electric heaters
Since its founding over 70 years ago, RAMA Industrial Heater Company has specialized in manufacturing and assembling electric heating units and devices. Today, all types, shapes and sizes of heating units are shipped from our modern factory to users throughout the nation.
RAMA, sales, engineering, and production personnel are highly trained, skilled, and experienced in all phases of heater design, engineering, and manufacturing. Their talents, ability, and pride of workmanship have led to our position as a leader in the electric heating industry.
In this booklet, we illustrate our facilities, products, and capabilities in the hope of giving you a clearer picture of RAMA, its plant, products, and people. We welcome your visit to our plant. Ample parking is provided on our large 12-acre site with over 40,000 square feet of manufacturing.
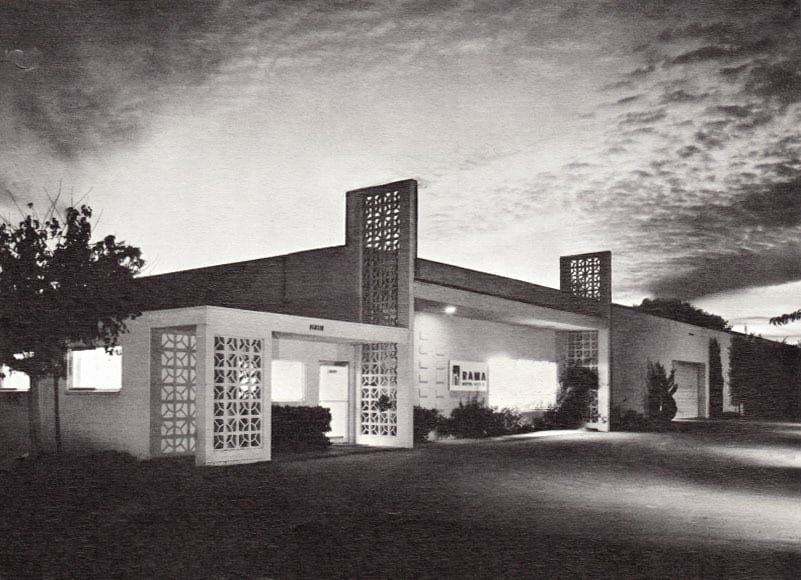
MANUFACTURING FACILITIES
The spacious RAMA factory is laid out for optimum production flow and personnel efficiency. Modern manufacturing, materials handling, and test and inspection equipment are utilized throughout production. Several special equipment items, unique in the industry, have been designed by RAMA to produce our heater products more efficiently. Innovations have also been made in materials and manufacturing techniques. These advancements have contributed greatly to continuing product improvement and the wide acceptance of RAMA heating products throughout the country. Instrumentation for thoroughly inspecting parts, sub-assemblies, and complete heater assemblies is in constant use in RAMA’s inspection program. Formal Quality Control procedures ensure that all heating units and assemblies meet stringent standards. A copy of our quality control manual is available upon request.
Cleanliness of parts, working areas, and storage areas is rigidly maintained. Pride of craft is continually stressed, and RAMA personnel are thoroughly trained and supervised in all phases of design and manufacture. Customer satisfaction is the prime concern of the RAMA management team. Insistence of thorough engineering, close customer liaison, and superior heating products has led to the success of RAMA . . . one of the country’s leading heating unit manufacturers.
ENGINEERING DATA
Included here is frequently used engineering information that helps determine heater requirements. More detailed information is available in our current catalog. If you have a heating problem, please contact us for assistance. Our engineering department is always available to assist you in any way in determining proper heater applications.
DETERMINING WATTAGE REQUIRED – basic formula
The energy to heat any substance = weight in lbs. X specific heat X temperature rise in °F = BTU
1 Kilowatt-hour = 3412 BTU mathematically expressed:

Specific Heat is the amount of heat necessary to raise the temperature of a substance by 1 °F. Expressed as BTU/lb.°F.
APPLICATION
The total wattage required to heat any substance consists of:
- ABSORPTION (watts consumed by the heated substance in a given time)
- HEAT LOSSES (radiation losses and losses due to absorption by surrounding enclosure, shelves, etc.)
- HEAT OF FUSION (if the substance is to be melted)
HEAT OF VAPORIZATION (if the substance is to be vaporized)
The best of fusion is the amount of heat required to melt one pound of the material. The heat of vaporization is the heat needed to vaporize one pound of the material. Each is normally listed in BTY/lb.
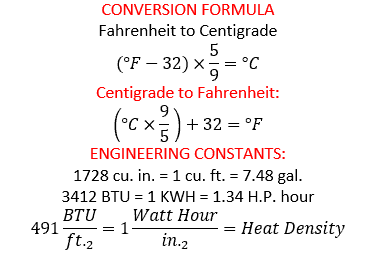
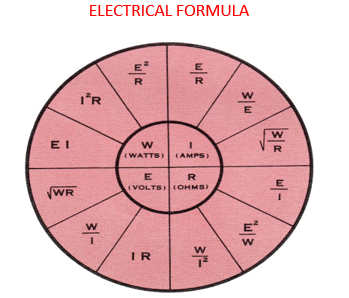
SOLIDS
Substance | Average Specific Heat BTU/lb./°F | Heat of Fusion BTU/lb. | Melting Point °F | Weight lbs./ft.3 |
Aluminum | .23 | 138 | 1216 | 160 |
Asphalt | .40 | 40 | 250± | 65 |
Bismuth | .031 | 23 | 520 | 610 |
Brass | .10 | …. | 1700± | 525 |
Brickwork and Masonry | .220 | …. | …….. | 140 |
Carbon | .204 | …. | …….. | ….. |
Copper | .10 | 75 | 1981 | 550 |
Glass | .20 | …. | 2200± | 165 |
Graphite | .20 | …. | …….. | 130 |
Inconel 600 | .126 | …. | 2500 | 525 |
Iron, Cast | .13 | …. | 2300± | 450 |
Iron, wrought | .12 | …. | 2800± | 480 |
Lead, solid | .031 | 10 | 621 | 710 |
Lead, melted | .04 | …. | …….. | ….. |
Nickel | .11 | …. | 2642 | 550 |
Nickel 200 | .12 | …. | 2615 | 555 |
Paper | .45 | …. | …….. | 58 |
Paraffin | .70 | 63 | 133 | 56 |
Rubber | .40 | …. | …….. | 95± |
Silver | .057 | 38 | 1761 | 655 |
Solder (50% lead – 50% tin) | .04 | 17 | 415 | 580 |
Steel | .12 | …. | 2550± | 490 |
Steel, stainless 304 | .12 | …. | 2550 | 495 |
Sugar | .30 | …. | 320 | 105 |
Sulfur | .203 | 17 | 230 | 125 |
Tin, solid | .056 | 25 | 450 | 455 |
Tin, melted | .064 | …. | …….. | …….. |
Titanium 99.0% | .13 | …. | 3035 | 284 |
Type metal85% lead15% antimony | .040 | …. | 500 | 670 |
Wood | .45± | …. | …….. | 40 |
Zinc | .095 | 51 | 787 | 445 |
LIQUIDS
Substance | Average Specific Heat BTU/lb./°F | Heat of Vaporization BTU/lb. | Boiling Point °F | Weight lbs./ft.3 | Weight Lb. Per Gallon |
Acetic acid | .472 | 153 | 245 | 66 | 8.81 |
Alcohol | .65 | 365 | 172 | 55 | 7.35 |
Ether | .503 | 160 | 95 | 46 | 6.15 |
Glycerine | .58 | …… | 554 | 79 | 10.58 |
Mercury | .0333 | 117 | 675 | 845 | 113.00 |
Oil, cotton-seed | .47 | …… | …… | 60 | 7.76 |
Oil, olive | .471 | …… | 570± | 58 | 7.75 |
Paraffin, melted | .71 | …… | 750± | 56 | 7.49 |
Sulfur, melted | .234 | 652 | 601 | …. | …… |
Turpentine | .41 | 133 | 319 | 54 | 7.22 |
Water | 1.0 | 965 | 212 | 62.5 | 8.34 |
GASES AND VAPORS
Substance | Average Specific Heat BTU/lb./°F | Weight lbs./ft.3 |
Acetylene | 0.35 | 0.073 |
Air | 0.24 | 0.075 |
Alcohol | 0.453 | …… |
Ammonia | 0.52 | 0.048 |
Argon | 1.24 | 0.104 |
Butane | 0.55 | 0.146 |
Carbon Dioxide | 0.203 | 0.123 |
Carbon Monoxide | 0.243 | 0.078 |
Chlorine | 0.125 | 0.20 |
Ethane | 0.41 | 0.083 |
Helium | 1.25 | 0.011 |
Hexane | 0.34 | 0.238 |
Hydrochloric Acid | 0.195 | 0.102 |
Hydrogen | 3.41 | 0.0056 |
Methane | 0.60 | 0.0447 |
Nitrogen | 0.245 | 0.078 |
Oxygen | 0.218 | 0.09 |
Propane | 0.47 | 0.164 |
Steam (212°F) | 0.482 | 0.037 |
Sulfur Dioxide | 0.155 | 0.179 |
NOTE: These values are approximate and only for 70 °F and atmospheric pressure. Specific heats and specific weights vary with temperature and pressure, so if your problem involves a material at temperature and/or pressure other than standard, these values may not apply. RAMA engineers maintain extensive data files on these and many other less common materials and will be pleased to help you whenever possible.